Discover the brands and technologies from our business units Henkel Adhesive Technologies and Henkel Consumer Brands.
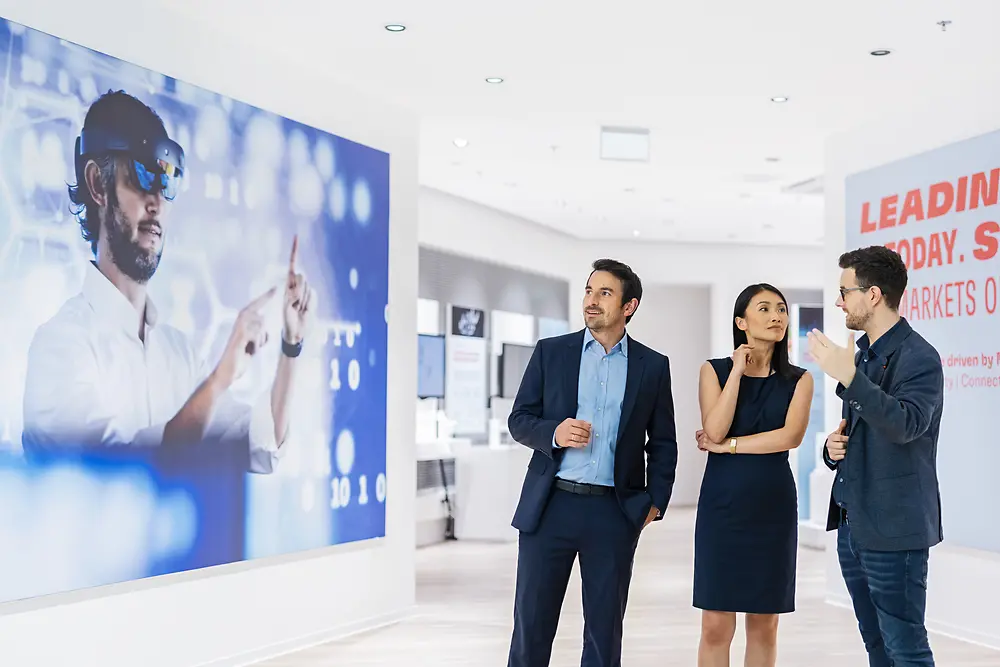
Inspiration Center Düsseldorf ICD
Our global innovation and customer center, where we develop adhesive solutions together with customers from over 800 industry segments.